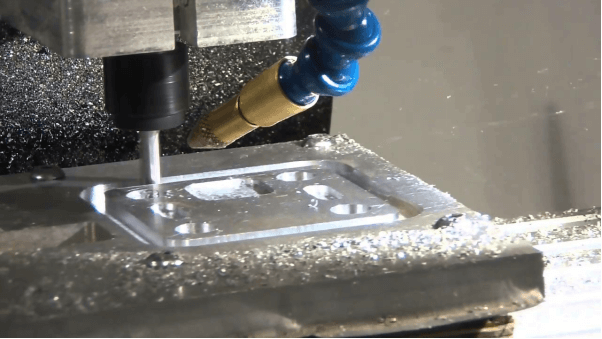
Common Milling Aluminum Machine Operations
Machine milling basically uses computerized controls alongside rotating machine tools to remove pieces of material from a workpiece to create a pre-determined product. This process may be used on different types of materials such as metals, wood, glass, and plastics. For example, when milling aluminum, there are various capabilities on how to mill aluminum including mechanical, chemical, electrical, and thermal processes. The main processes include drilling and turning.
In this article, we will look at the basics of the milling processes, the different milling operations, as well as the material considerations.
The milling process
As we mentioned earlier, milling uses computerized controls that control cutting tools that cut out shapes from the workpiece.
The process starts with the creation of a CAD design either in 2D or 3D. The design is then converted into a file format that is compatible with the milling machine – this is what controls the movement of the cutting tool. After, the workpiece is loaded onto the machine’s work surface and then the milling process starts. The cutting tool rotates at high speeds that could reach thousands of rotations per minute.
Here’s what the machine does to produce the pre-determined cuts:
- Slowly feeds the workpiece into the rotating tool while its at rest
- Moves the cutting tool across the stationary workpiece
- Moves both the tool and the workpiece in sync with one another
Common Milling Machine Operations
Machine milling is best suited for producing high precision parts in products. The concept is used in a wide range of industries to make various parts and designs. The most common milling operations are:
- Face milling
- Plain milling
- Angular milling
- Form milling
- Straddle milling
- Gang milling
- Profile milling
- Gear milling
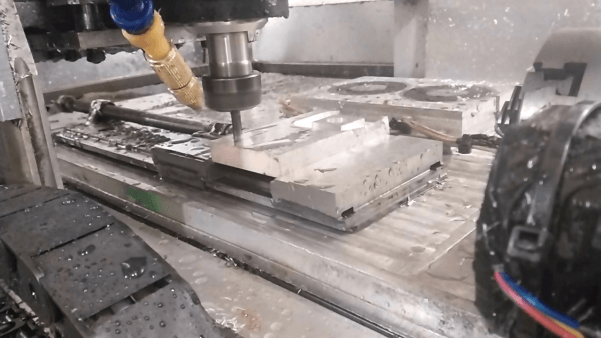
Different Types Of Milling Machine
There are different types of milling machines that have different applications and uses. The common types of milling machines based on the combination of their specific characteristics are:
- Knee-type
These have a fixed spindle and a worktable that can be adjusted vertically. The worktable rests on the saddle and is supported by the knee which can either be lowered or raised depending on the position of the cutting tool
- Ram-type
These have a spindle that is fixed to a movable housing which makes the cutting tool to rotate on an XY axis.
- Bed-type
These machines use worktables that are directly fixed to the machine’s bed. This makes it impossible for the workpiece to move about either in the X or Y-axis.
The bed-type machines are either available in simplex, duplex, or triplex depending on the number of spindles.
- Planner-type
These machines are quite similar to the bed-type machines in relation to the worktables. Both machines’ worktables are fixed. For this particular type, the worktable is fixed along the X and Z axis while the spindles move along the XYZ axes.
The Material Considerations
Milling is done on workpieces that are either metallic, plastic, ceramic, glass, or elastomers.
When choosing a material that is best suited for your machine, you need to put into consideration the properties of the material such as it’s hardness, resistance, tensile strength, as well as the chemical and temperature resistance. Do not forget to consider the cost-effectiveness of the material too.
The material that is chosen affects the functionality of the machine in terms of cutting speed, depth of cut, feed rate, and the design of the final product.