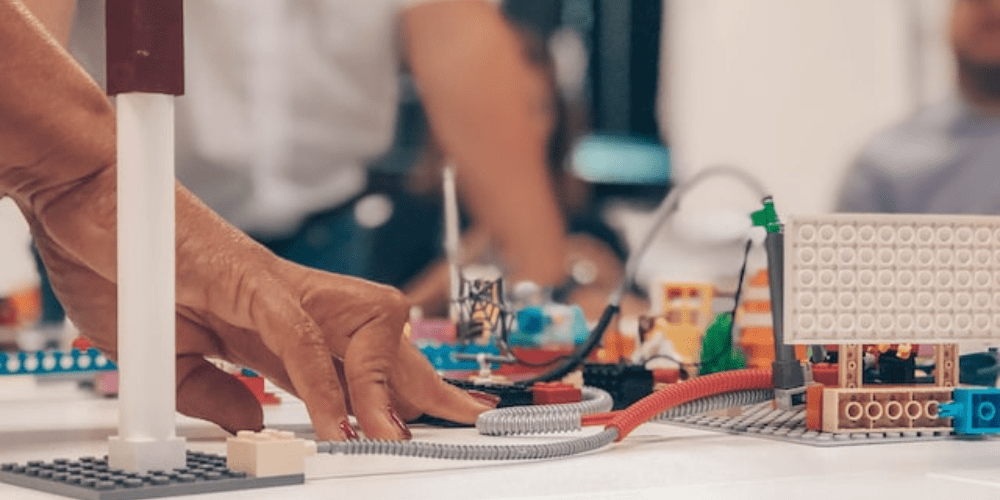
There is more to CNC machined prototypes that you don’t know!
CNC prototype machining has been the talk of the market for the past few years. It is the newly emerged technology to support low production for prototyping compared to other metho
CNC prototype machining has been the talk of the market for the past few years. It is the newly emerged technology to support low production for prototyping compared to other metho
The single-man aluminum mast lift is mostly famous for its lightweight and high lift. It is made of aluminum alloy. So, the weight of the lift is light. The operator can move it qu
If the first thing that comes to mind when you hear about a foldable house is one that folds, then you’re definitely not far from the truth. Yup, that’s right; there are houses
Bottle printing can be quite beneficial for your company, whether you’re seeking for a low-cost approach to improve brand visibility or want to use bottle labels to forge an
If you’re a jewelry designer, the co2 laser engraving machine is the tool that will make your life easier. The CO2 laser can cut and etch wood, plastic, and glass. It also wo
While the world would be much better if we ate french fries every day, it’s not always practical to make them yourself. But there’s good news: you can get crispy, delic
Engineers have been essential in keeping Australia’s economy afloat amidst the pandemic. This is because it boosted, supported, and empowered the mining industry to be in busines
A thermowell is defined as a pressure-tight receptacle device that is constructed to accept a temperature sensing constituent. It offers a way to introduce that constituent into a
All industries are not made equal, but one group of professionals are important across all fields — engineers. Where would the world be without engineers? Impossible to imagi
Neodymium magnet or ndfeb magnet consists of Neodymium and boron and iron alloys. It has excellent properties and is the strongest type of magnet used in industrial applications.