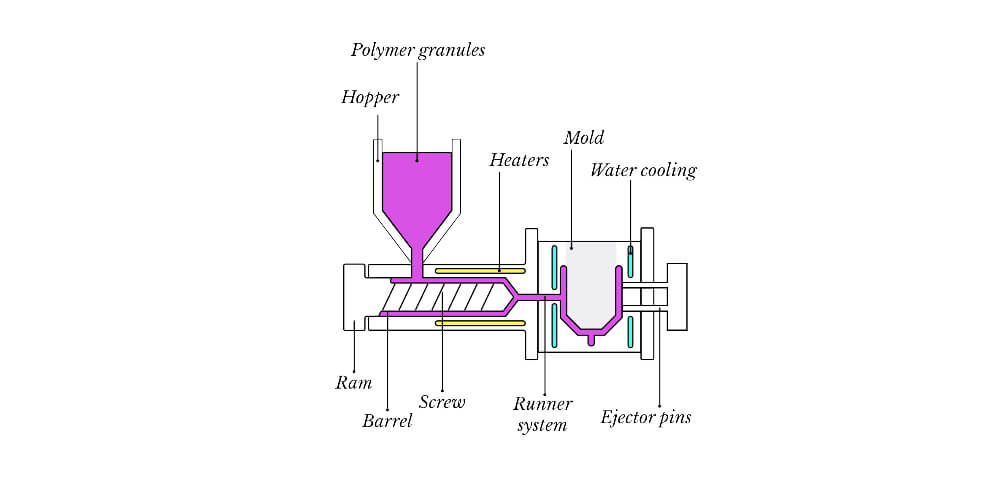
What is Plastic Injection Molding?
Plastic Injection Molding is one of the most used manufacturing processes used to fabricate plastic parts. It is the process by which pellets are melted, injected into an injection molding design, and cooled to desired designs. Custom plastic injection molding service is used to manufacture a wide range of products depending on their use and size. For the process to be successful, raw plastic materials, mold, and an injection molding machine need to be present. But, before you get your machined part projects started today, understand what entails this plastic injection molding works first.
The Process of Plastic Injection Molding
Once you assemble all materials, the next thing is choosing the injection machine that suits your needs. After selecting an injection machine, put in plastic raw materials to be melted and into the runner system.
Below are the four stages involved in the process
· Mold Clamping- The mold is made of two halves. The two halves are firmly secured to the injection molding machine.
· Injection- Raw plastic materials in the form of pellets are put in the machine. In this process, the pellets are melted by heat and pressure, after which it gets injected into the mold.
· Cooling- After the melted plastic comes into contact with the inside of the mold surface, it starts to cool. As it cools, it takes the shape of the desired part.
· Ejection- After it has cooled, the cooled part gets ejected by the ejection system. When the mold is opened, it automatically pushes the cooled parts out.
How to Minimize the Cost of Plastic Injection Molding
Since the cost of injection plastic molding depends on several factors, such as materials and the size, it’s essential to go with simple mold designs, small mold sizes, and use aluminum tooling since it can be produced in low-volume.
To run efficiently, choose a plan that can be manufactured with ease, ensure there’s enough room for design, and choose the best quality of plastic materials.
Things likely to go wrong during Injection Molding
The injection molding process uses heat, and a lot of things are likely to go wrong. The problems can be fixed with the presence of experienced engineers. The issues include burn marks, discoloration, flow marks, sink marks, and weld lines, to name a few.
Benefits of Plastic Injection Molding
· Compared to other methods, it is the fastest method. The time used from one cycle to next is less than a minute. Large volumes of molds can be produced within a short period.
· Injection molding can produce complicated parts in uniform. It can produce identical parts.
· The process uses automatic machines; this means minimal staff is needed to supervise the process.
· It is a stable and reliable process that can be trusted to produce high-quality parts.
· Products made from the injection molding process tend to last longer.
Final Thoughts
Plastic Injection Molding is a process that is used by most manufacturers around the globe. Different manufacturing processes, such as insert molding and thermoplastic injection molding, are used. Since it is a plastic injection molding process, it doesn’t mean only plastics are used, materials such as Polycarbonate injection molding and ABS plastic molding are used. Among the plastic materials, ABS is the best since it can be molded with ease, and it has uses in different industries.