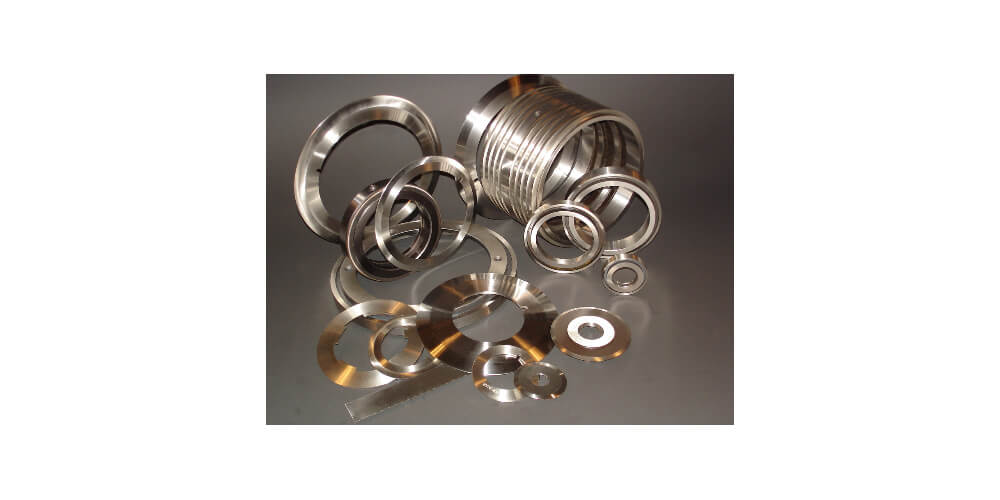
A Closer Look at the Common Slitting Methods
Razor, shear, and scoring are three of the common types of slitting methods used in material conversion. Every process is utilized on a material that can be optimized, via a proper blade selection. Slitter blades sum up the equation.
What slitting method is right for your industrial needs?
As companies start the process of buying a custom slitter rewinder system, they soon realized that the right answer to this question is imperative to the machine type designed and built for the application of the company.
Experts hold that focusing on a customer’s application parameters and keeping cost and safety in mind are some of the essential factors to consider when choosing a slitter for the job.
Thus, to save money, the overall converting operation should be studied. The slitting and rewinding procedures are the ideal place to look.
Having the right device for the job is a huge saving any converter can have. Before you buy a converting machine, you should determine the right slitting method for your machine.
Some of these methods can cause a different reaction to your material, causing frayed edges and stretched materials. Experts in the slitting world recommend that you send a sample of the material before the quoting process starts.
Here is a brief rundown of the common slitting methods.
Razor slitting
Razor slitting is a simple, cheap method. It is also easily adapted to any machine type, in any location.
The cutting or slicing action applied is created by pulling the material slightly past the blade. As a result, stress is induced into the fracture.
One advantage of razor slitting is that it creates a controlled crack in the slitter blade.
The mechanical properties of used material coupled with the shape every blade takes determine how and where the crack is to form
If the crack forms into the blade edge, the process is stable. However, if it forms ahead of the material’s tip, the process can be unstable (flaws may develop).
Shear slitting
Shear slitting is one of the most versatile slitting methods on the market. It can accommodate a broad range of materials as compared to other slitting methods. A clear shear stress may be formed when the material passes through the tip of the nip formed by the blade.
Determining and establishing the correct cut point is complex. Many people may hardly understand it. A proper nip configuration considers the following factors:
- Web path
- Blade edge
- Blade overlap
- Trim removal path
Anytime the shearing nip is configured properly, a slit quality is unsurpassed. A properly sheared slit edge, if viewed properly under the microscope, will display the impacts of a real shearing stress in the material. Pronounced differences will also be highlighted.
Score slitting
Score slitting is one of the least common methods of slitting metal. It is dusty and delivers poor edge quality.
Stress forms within the crushing nip right between the anvil and the wheel. Slit quality has a variation that depends on the material being used.
Final Thoughts
Of the three slitting methods, a razor is the most affordable. It is also the simplest as well as the cheapest method. For most people, it is easily adopted to any machine type.