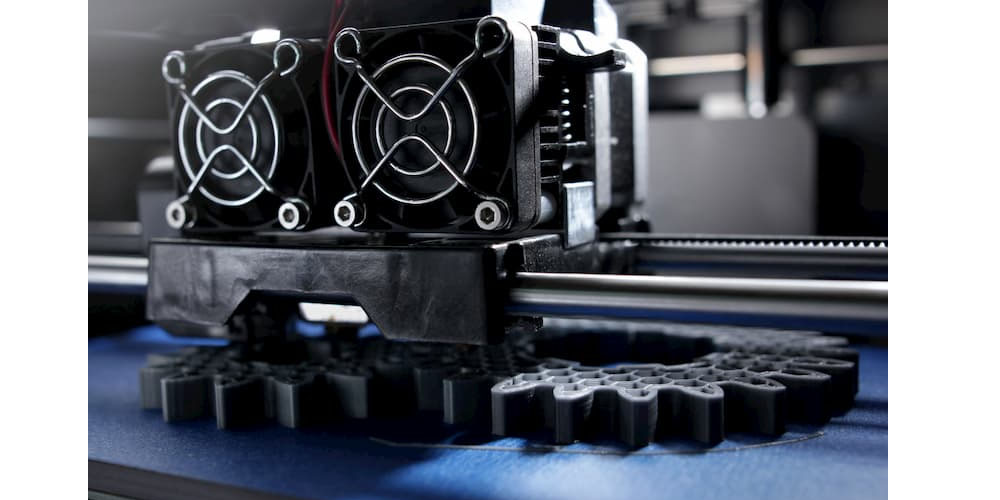
Importance of the Two Types of Rapid Tooling
The primary goal for most manufacturers dealing with product development is prototyping and mass production of objects. However, a prototyping company can concentrate on low-volume manufacturing for industries like aerospace and automotive, which involves rapid tooling, CNC machining, pressure die casting, and others. Rapid tooling is a process that incorporates additive manufacturing to develop tools and speed up their production. It is a cost-effective technology producing parts in small volumes depending on the technique used. In this post, we discuss the forms and benefits of rapid tooling.
Forms of Rapid Tooling
Rapid tooling is divided into two forms, i.e., direct and indirect tooling. Successful application of rapid tooling techniques in prototyping requires an understanding of both types.
1. Direct Tooling
This type is applied most in manufacturing, but some designers still use it in prototyping. Tools are manufactured from Computer-Aided Designs to produce molds that are later used to form actual products. Direct tooling uses few resources, and it’s a short process, so only a few steps are involved. When one mold is created, it is used to develop several prototypes, reducing costs and time.
As much as direct tooling has benefits, it also has drawbacks. Many designers prefer not to use it since it has limited uses. Also, the development of errors in the product dimensions is high since no pattern is used. Direct tooling isn’t ideal for parts with complex designs, and the products produced are not durable.
2. Indirect Tooling
The process uses additive manufacturing to create three-dimensional objects. A specific pattern is used to make tools, so it’s easier to work on detail or complex designs, unlike with direct tooling. The pattern involved is durable and can be reused without damages. You can use the pattern to develop many test tools using various materials. Indirect tooling is common in prototyping, but CAD is not applied. If the design appears faulty during the process, no correction can be done immediately. The entire pattern must be replaced and the process restarted. It is also costly and time-consuming due to the many steps involved.
Benefits of Rapid Tooling
Generally, rapid tooling has several advantages that cut across all types and techniques. They include;
1. Cost Saving
Before mass production of products is done, one prototype is made to represent the final product. If any errors in the design are present, fixing it is easier and less costly than when a whole batch is faulty.
2. Time-Saving
Rapid tooling is a quick process, unlike conventional tooling, which takes a lot of time and requires special patterns and tools. The steps involved are few, so the product gets to the evaluation level fast. The customer can also give feedback immediately after testing, and the products can be introduced to the market sooner.
3. Opportunity to Invent
As a designer, you can develop new design ideas for products, whether simple or complex. Creating animations is possible than in conventional tooling.
Bottom Line
Rapid tooling has been beneficial to the product development industry in prototyping and manufacturing. It is fast and easy and requires fewer resources. Choose the ideal form of tooling before starting the production process or seek assistance from an expert.