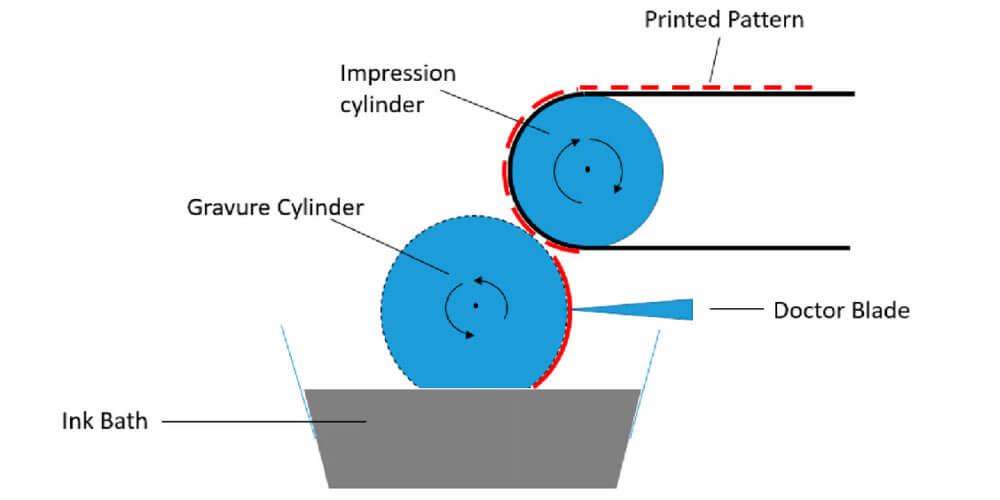
The Inner Workings Of The Gravure Printing Process
The Gravure printing process is a type of intaglio printing process. It makes use of gravure printing cylinders, which rotate while printing. The cylinders are etched to create a picture or image that is printable on a surface. Thus, to make etching easier, copper-plated cylinders are used. The entire process takes a short amount of time considering the workload produced and the print quality. Gravure printing is used to print out magazines, newspapers, and some types of packaging materials for brands. This article discusses the details of the gravure printing process. Most printing plants use the same process, while some make slight variations to differentiate their products.
Step 1 Design development
The first step of any printing process is coming up with a suitable design. The client needs to decide the kind of font to use and the colors used for the printing. Some printing companies have a design department to help in completing the designs.
Step 2 Pre-press
The Rotogravure printing industry uses the term pre-press to describe the many processes between design creation and the final printing run. This stage is essential because printing millions of copies requires extra care to avoid making costly mistakes. Some of the processes that happen here include the manufacture of printing plates and image form.
Step 3 Galvanoline
Gravure printing uses cylinders that are manufactured or prepared at this stage. The quality of cylinders is a perfect indicator of the quality of print achieved. Flawless production depends on the perfect execution of this step. Staff should also get trained in using modern equipment with high standards of artistry.
Step 4 copper polishing
Manufacturers use a polish machine to prepare the copper surface. Polishing the copper ensures limited resistance and even cylinders. The polishing machine uses software to give the cylinders a perfect polish.
Step 5 Rotogravure engraving
This step requires the utilization of electronic engravers for a seamless finish. This step is crucial for the perfect outcome. The ideal desired outcome lies in the balance here, which is why highly trained professionals use the electronic cutter to engrave at different angles and patterns for the best result.
Step 6 Chrome plating
For the cylinders to last longer, they are dipped in a chrome bath. The bath is used as soon as the engraving is done to prolong the life span. You would not notice the difference because chrome has an appearance similar to copper.
Step 7 Proofing
This part of the printing process allows the client to inspect the print pattern and design. Some companies will skip this step because they trust the printing company. Companies need to check if their requirements are met at this juncture because, after this, any printing mistakes can be costly.
Step 8 Quality assurance
Quality assurance is taken care of by the printing company. Inspection is easy with experience; the longer the company has been in business, the easier it identifies mistakes and makes corrections.
Conclusion
These stages result in the production of a perfect representation of the clients’ wishes. The gravure printing process gets the client’s printed material with several advantages: cost efficiency, high quality, and impressive speeds. Working with a trustworthy printing company reduces the risk of making any mistakes and delayed deliveries.