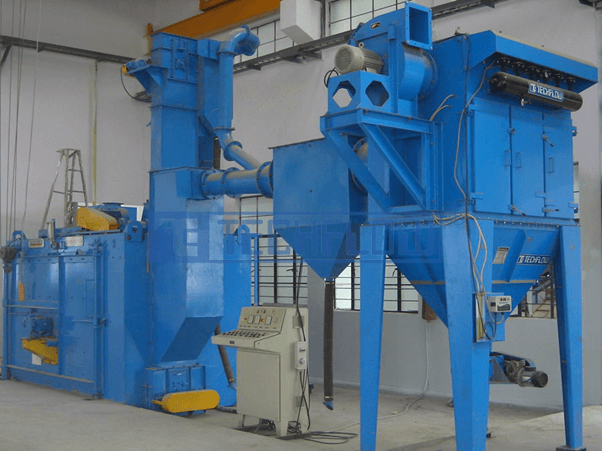
What Are The Top 3 Shot Blasting Defects? Describe Them
Defects or imperfection in metal structure can contribute to the growth of a toxic environment. Metal defects can also primarily impair the chemical and physical properties of the said metal. For that reason, there needs to have a distinction made between major metal defects with a beautiful structure and the coarser defects. That is why, typically, as an individual seeking to invest in the shot blasting industry, you need to focus on factors that can contribute to the development of metaL defects. So in this blog post, that is what we majorly highlight.
Metal defects, specifically in the blasting sector, have a way of polluting the environment too. That is why you need to contain them into one docket as a preventive measure. That said, the defects in different metals such as welds and sharp edges are the major cause of failures in the coating. They will interfere with the standard performance of the metal, thereby giving automatic low-quality results. It is, therefore, crucial to identify different surface defects prior to indulging in the blasting process.
Corrosion
Usually, the defects located in the metal are distinguished based on their size as well as location and origin. These defects can easily form when there is the smelting of metal or during casting production. So, as a person working in the blasting sector, you should be familiar with all processes that cause metal defects. While at it, coarser metal defects are pretty much microscopic. They cause disturbance to the center of the metal, thereby interrupting its ability to function correctly.
Erosion
The defects in blasting are categorized in size. This implies that some defects are significantly more significant than others. Therefore, your decision to pick the right one entirely depends on the size of the metal defects. So even if there is a meTAL defect you have spotted in the blasting process, you could always have a viable solution to it.
In the next paragraph, we shall look at the solutions to metal defects.
Inspection
If you want to evade metal defects during blasting, then you should inspect the site before anything else- the abrasive blaster in charge of investigating the elements used for blasting needs to be checked. After that, it would be best if you weighed in on the possibilities of carefully selecting the visual scan specifically for any existing cuts and indicators.
Other than that, there is also a grading system you can consider using in the process of assessing the blasting area and the materials used. So, it is pretty much necessary to consider using the skills of a professional in the long run.
Take-Home
Metal defects can compromise your operations in many ways. Therefore, you need toweigh in on the options to use when blasting begins. Consider hiring a professional or Tech Company that can assist you in seeking the right services for operations. It would help if you also worked with professionals skilled in going through the recommended blasting processes.