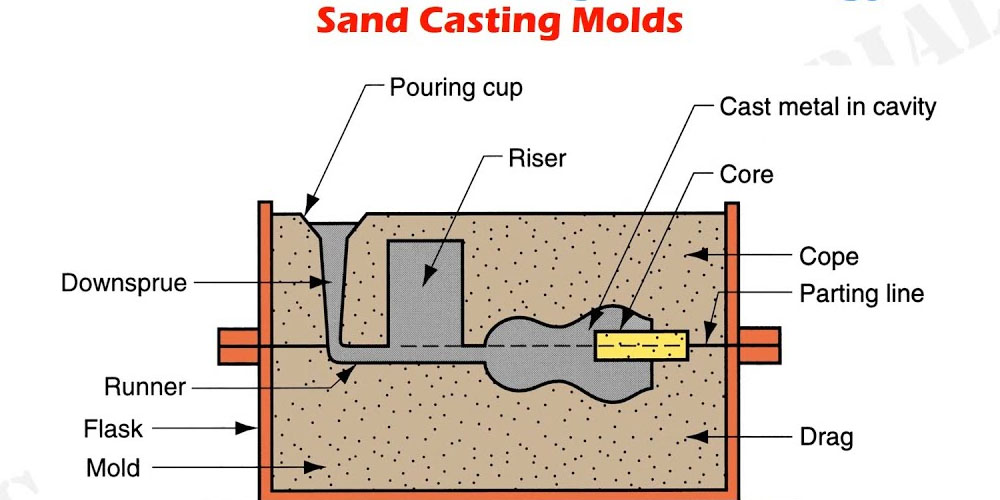
The components of the sand casting process
Sand casting is one old casting technique, where non-reusable molds made of sand are used to make metal castings. It is a complex yet straightforward production method used to make metal components of varying sizes. The technique can be used for making complex products with intriguing details. Sand casting parts are a significant part of the process. For this reason, in this write-up, we discuss sand casting components.
The components of sand casting
A good sand casting mold is significant for the success of the sand casting process. This means that the first thing you need for the sand casting process to be successful is a good sand casting mold. A good mold features multiple parts that work together to achieve the final product. Below are the parts of a sand casting mold;
1. The patterns
This is perhaps the essential part of the sand casting process. This is because it is the first step of creating the mold, which is at the core of the process. For this reason, the patterns are the first components to be manufactured during the sand casting process.
2. The mold
This part is usually created from the patterns. It features the design of the final product. Therefore, it is equally as crucial as the patterns.
3. The core
This is a sand shape. It is typically inserted into the mold. The core role is to shape the casting interior to create holes, also known as the passages. This part is typically made from molding sand because the sand can be shaken out of the casting once the molten metal has cooled down and solidified.
4. The core print
This is the region that is added to the pattern or mold. Its role is to locate and support the core. It is usually located within the mold.
5. The molding sands
This is the sand used to create the mold. The sand is usually prepared in mullers. The muller mixes the sand with a bonding agent and water. This combination helps the sand withstand the pressure from pouring the molten metal. This means that the sand won’t loosen when the molten metal hits it.
6. The furnace
This is the part where the metal or product material is melted. It is worth noting that sand casting involves metals with high melting points, like nickel, titanium, and steel. Therefore, the temperatures at the furnace are usually very high. In some cases, the temperature in the furnace can be adjusted depending on the material.
7. The shakeout station
This component uses techniques like vibration to shake off the sand after the molten metal has cooled down and solidified. Aerators are used inside the shakeout station to loosen the sand. The aerators make the sand more amenable to the molding process. The sand removed at this part is returned to the storage bin, where it can be reused.
Final word
Sand casting is a very beneficial technique because the part size does not restrict it. As long as a suitable mold is created, it can make parts of any size. It is also simple and can be used to make complex parts.