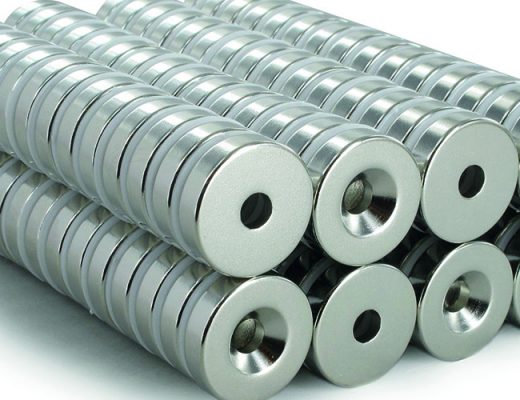
Two Processes of Forming Neodymium Magnets
Neodymium magnet or ndfeb magnet consists of Neodymium and boron and iron alloys. It has excellent properties and is the strongest type of magnet used in industrial applications. It has been in existence for decades and still tops the magnetic chart with its performance due to its strong magnetic field. There are two types of Neodymium magnets, named according to how they are developed, that are bonded and sintered magnets. In this post, we delve into the processes of forming Neodymium magnets.
Processes of Forming Neodymium Magnets
There are two distinct ways of making Neodymium magnets; bonding and sintering
1. Bonding
The process is also referred to as compression bonding. It’s a procedure where die pressing is used alongside a binding mixture of Neodymium and Epoxy. After proper mixing, the mixture is cured in an oven or compressed using a press machine. The resulting magnets are configured in different shapes depending on the client or manufacturer. The bonding process is short, and the magnets don’t require further processing since they are isotropic and have a high tolerance.
2. Sintering
It is the second method of making the magnets and involves multiple steps.
a. Melting
The metals needed to make the magnet, Neodymium, Boron, and Iron, are put in portions into a furnace to melt. The manufacturer ensures all portions are in and then adds elements like cobalt to enhance corrosion-resistant properties. An alloy is created during the melting process; however, it is not made to standard as different manufacturers add different elements.
b. Powdering of the Alloy
Once the alloy is melted completely, it is cooled and molded to form ingots. They are then placed in a concoction of nitrogen and argon and jet-milled into powder form. It is later moved to a hopper for pressing.
c. Powder Pressing
In the hopper, the powder undergoes pressing, forming a giant die. The large size gives it room to reduce to its original size and shape later. It is placed in more die and exposed to a magnetic field to acquire magnetic properties. Demagnetization is later done using a pulse to rid the magnet of its properties, and a green magnet is created.
d. sintering and Machining
In this step, the green magnet is heated in an area with no oxygen below its melting point. The process helps the magnet acquire its magnet properties and behave like an actual magnet. The formed particles become adhesive at 1080 degrees temperature and then cooled, ground. The magnet is then cut and shaped to the desired shape.
e. Plating, Coating, and Magnetization
The coating uses components like copper, zinc, and nickel to prevent wear and tear from corrosion. A strong magnetic field is directed to the magnet using high voltage levels, and a strong current is produced
Bottom Line
Neodymium magnets have unmatched magnetic properties achieved via the two processes discussed above. One significant benefit is having them made in your preferred shape and size as long as they retain the performance and strength. Select the process that works best for you and seek assistance from the manufacturer.