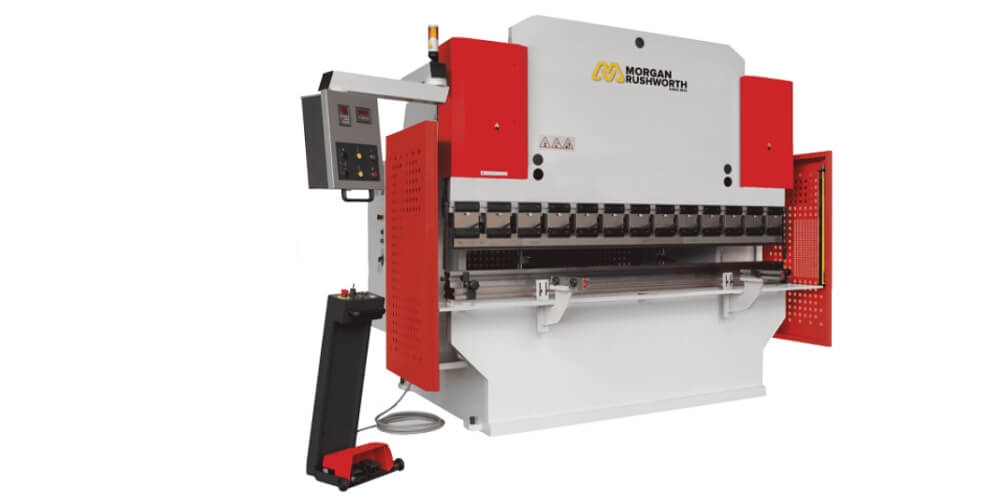
What is CNC Press Brake Forming?
In most manufacturing machine shops, press brakes play an important role in the metal forming process, these devices use force application to shape different solid metal objects, and they are commonly used to bend sheet metals at a particular angle.
Over the past several years, the cnc press brake forming has changed to suit new manufacturing businesses. Therefore, it can be challenging when it comes to generalizing the manufacturing machines. It is important to understand the following concerning the press brake forming technology:
Press Brakes Application options
Different press brakes are designed to apply force on the workpiece in various ways. That is because they have unique operating mechanisms that require different ways to maintain them. The following are types of press brakes according to the ways they apply pressure:
Mechanical
It is the oldest press brake technology form, and it bends objects using a flywheel that is by powered by a motor to produce and supply the required force.
Pneumatic
They use air pressure to enable their rams to move up and down, and their ton limit is lower than the hydraulic, bringing about their difference.
Hydraulic
These press brake rams get in motion due to the hydraulic fluids filled in the cylinders to work on the material shaping. They are considered to be more accurate than the mechanical ones as one can easily adjust them to fit individual depths.
Servo-electric
They are equipped with an electric motor that drives the ram, and they are fast and efficient than other technologies. That is because they are suitable to working on low tonnage pieces. They are easy to maintain as they do not have hydraulic or any other oil.
The press brake parts
The parts of CNC press brake vary depending on the design of the machine. Also, they depend on the drive system they use. Normally a press brake has the following components:
- The bed, where the workpiece rests
- A ram that pushes the piece down
- Dies that helps in metal shaping
- A back gauge that ensures the bend is on the right spot
- A CNC system, however, the older machines do not have this feature, but the ones made over the previous decade are equipped with the system
Bending operations
There are two primary types of bending operations that a press brake can perform: air bending and bottoming. Bottoming operations force the workpiece to the die. This is necessary to ensure it conforms to the die’s shape making it more of coining operations.
The main advantage of bottoming is that it attains bend accuracy depending on the die’s shape; therefore, the brake does not need to be more precise to get the required accuracy. However, it needs more force application making it the best option for high tonnage press brakes.
Having a clear understanding of press brake forming technology will enable you to get the right services for the right materials you want to shape. This will reduce the chances of creating wastes due to working with the wrong specifications.