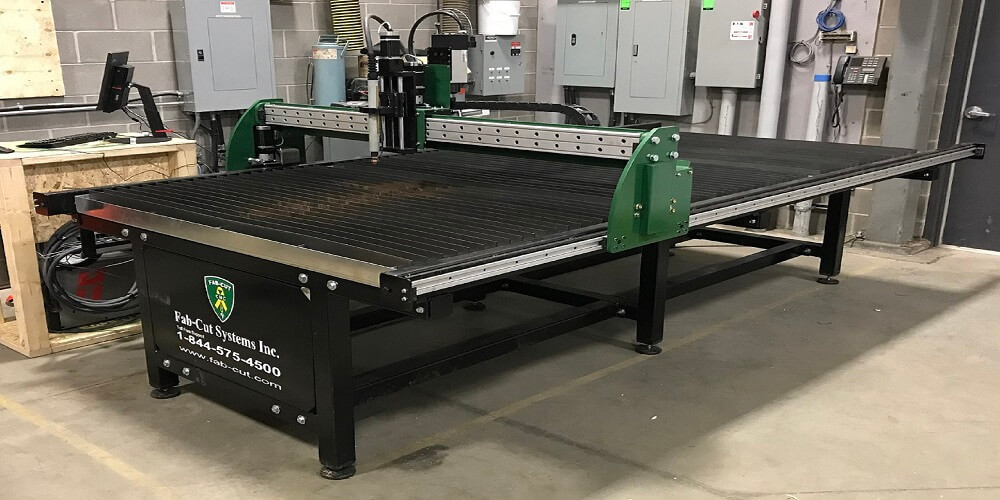
Why Plasma Cutting Machines are the Best
Plasma cutting machines are powerful machines that can be used to cut various materials. The principle by which this machine operates is by causing gas to reach the fourth state of matter (the plasma state). This is done by passing an electric spark through the compressed gas, thus causing the gas to reach the plasma state. As a result, the plasma steel cutting machine burns hot enough to cut through steel.
Plasma cutting machines can use different gases to cut through various materials. Some may use nitrogen or other consumable gases. When the plasma is created, it then transfers an electric arc between the material that is being cut and the cutter’s power supply. Thus, whenever the plasma touches the workpiece, intense heat is generated which can be used to cut through different materials.
The major advantage of using plasma cutting machines is that they do not cause warping or bending of materials that are usually common with materials cut with physical force-based cutting methods. Instead, they offer smooth and very precise cuts in various materials. However, they can be utilized in different ways. Here are a few ways plasma cutting machines can be utilized.
1. Cutting Tough Materials
A major drawback with using a cutting blade to cut high-hardness materials is that the cutting blade can become dull quickly. In the process of cutting through metal, the saw quickly gets dull. It can also cause hazardous sparks in the workshop. Besides, in the process of cutting through metal, you can have metal chips flying around.
Plasma cutting machines, however, are not subject to wear and tear. As such, they can keep cutting through touch materials all day. As long as there’s sufficient gas to turn into plasma, the machine can keep working non-stop. Hence, there will be no need to shut the machine down at intervals to replace the tooling. This ultimately saves time, especially when there are lots of materials to be cut.
2. Rapid Cutting Jobs
Another great advantage of using plasma cutting machines is that they are ideal for cutting jobs where efficiency and speed are crucial. For example, there is no need to preheat the torch as you would with an oxyacetylene torch. Also, you will not need to constantly change the tooling of the machine as you would with physical cutting tools. As a result, this machine is ideal for cutting jobs that need to be done as fast as possible.
3. Reduce the Heat Affected Zone of a Cut
When cutting materials with a thermal-based cutting method, you have to deal with the heat-affected zone (HAZ). The physical properties of a material may be altered as a result of a large amount of thermal energy the material is exposed to. Some metals are deliberately exposed to high temperatures for this reason.
However, this often causes the material to be brittle. It can also lead to warping. Using a CNC plasma cutting machine helps reduce the heat-affected zone to ensure that the physical properties of the material are unchanged. It also ensures that the cuts are neat and straight.